Carbon Fiber Parts Manufacturing
Home > Capabilities > Carbon Fiber
What is carbon fiber molding?
Carbon fiber molding process is a process in which carbon fiber reinforcement and resin matrix are molded under high temperature and pressure in a mold.
This process combines the high strength and lightweight characteristics of carbon fiber materials and is widely used in aerospace, automotive manufacturing, sports equipment and other high-performance fields.
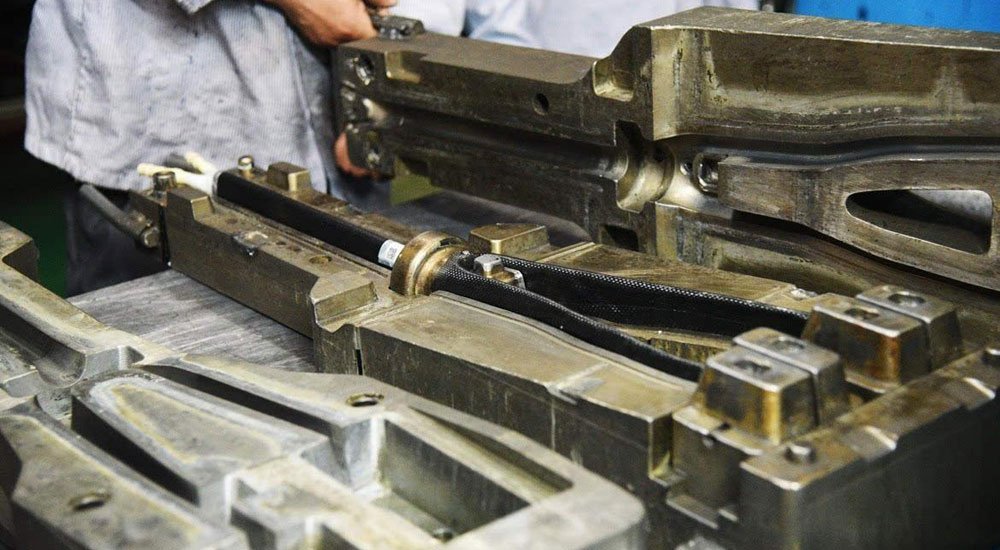
Main steps of carbon fiber molding:
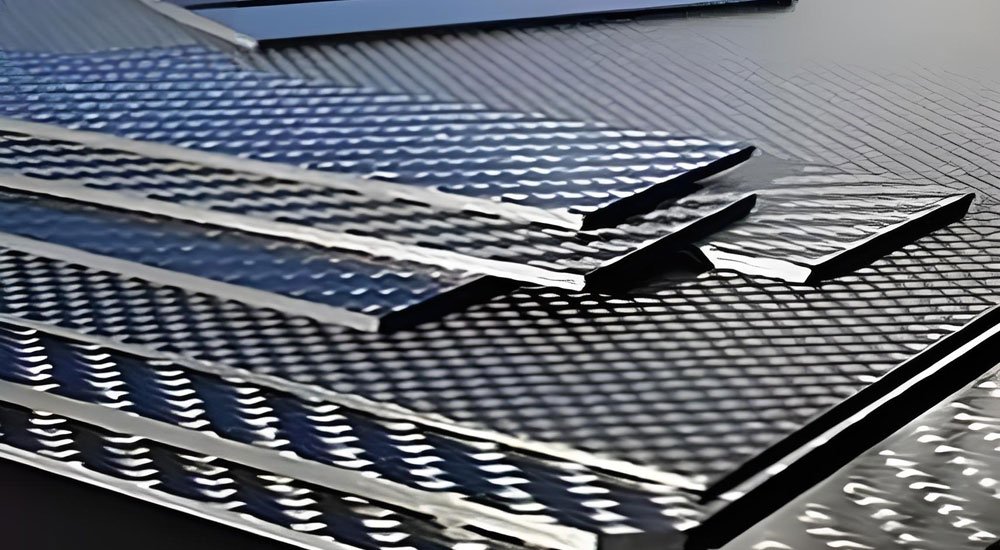
Material preparation:
Prepreg or carbon fiber fabric is selected and cut to the desired shape according to the design requirements. Prepreg is a sheet of carbon fiber pre-mixed with resin to ensure the proper ratio of resin to carbon fiber.

Mold Preparation:
Molds are usually made of metal (e.g. steel or aluminum) and must have good heat resistance and precision.
The surface of the mold needs to be treated smooth and coated with a release agent to prevent the material from adhering to the mold after molding.
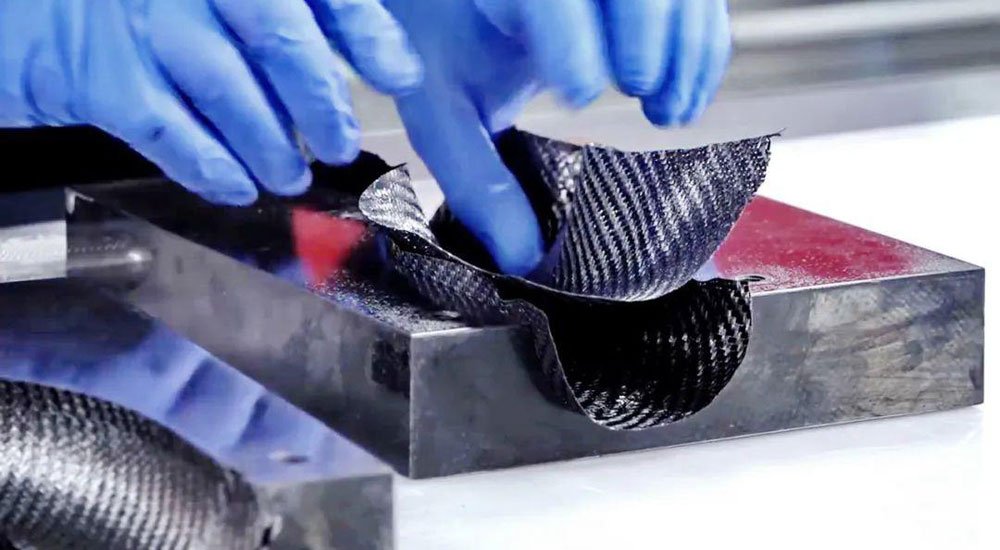
Layup:
The cut carbon fiber material is laid in the mold, which usually requires multiple layers according to the design requirements to ensure the strength and performance are up to the demand.
Different layup angles of the layers can optimize the mechanical properties of the composite.
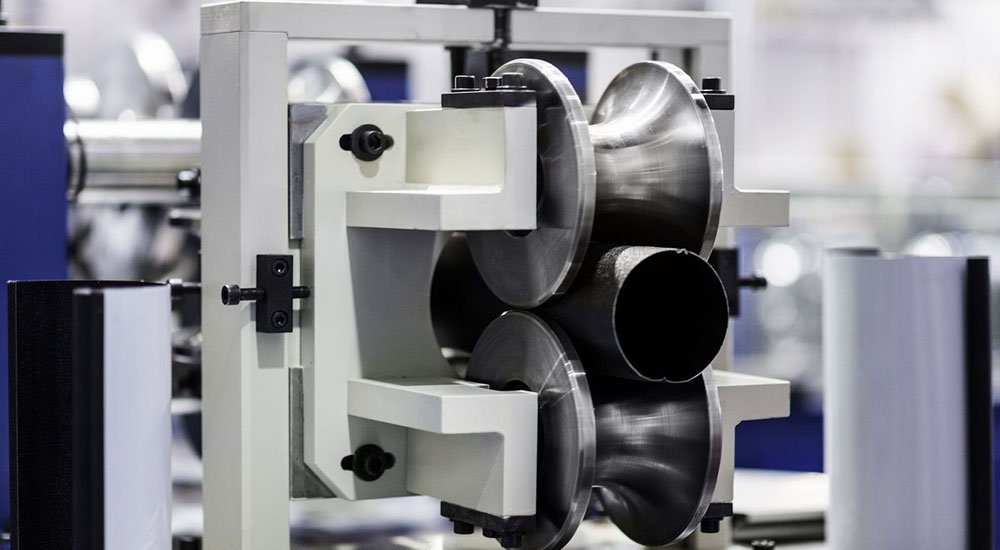
Molding:
Carbon fiber and resin are pressed into shape by heating and applying pressure with the mold closed.
Temperatures are typically controlled between 120°C and 180°C, and pressures range from 3 to 5 MPa. Heating times and pressures depend on the type of resin used and the thickness of the part.
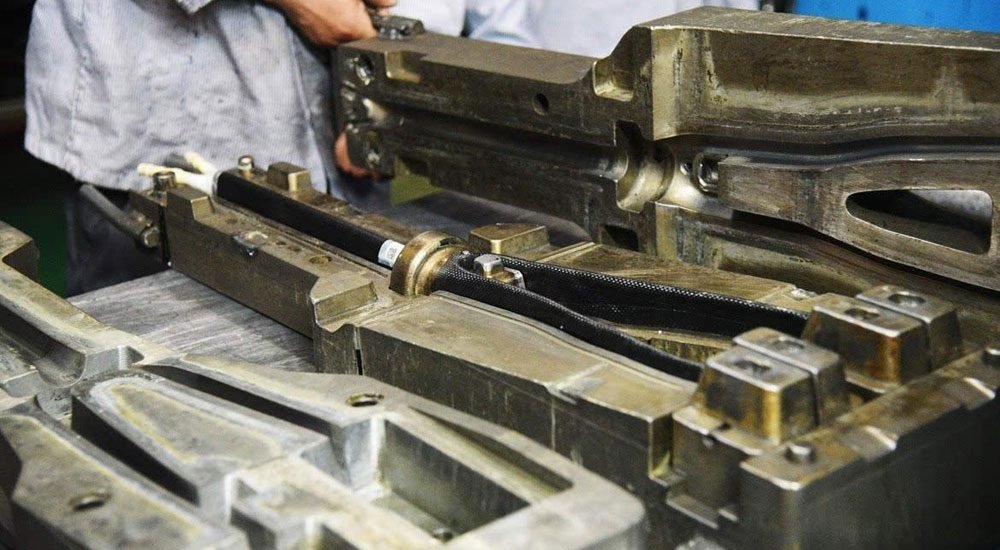
Curing:
Under high temperatures and pressures, the resin undergoes a chemical reaction and gradually cures to form a hard composite structure.
Curing times typically range from 30 minutes to several hours, depending on the material and process parameters.
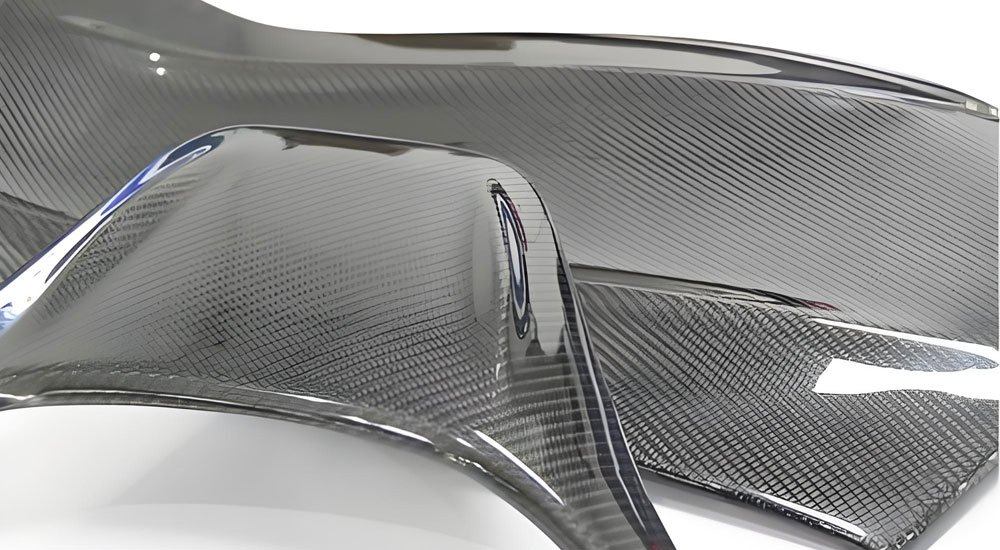
Demolding:
After molding is complete and cooled, the mold is opened and the finished product is removed from the mold. At this point, the finished product has good dimensional accuracy and surface finish.
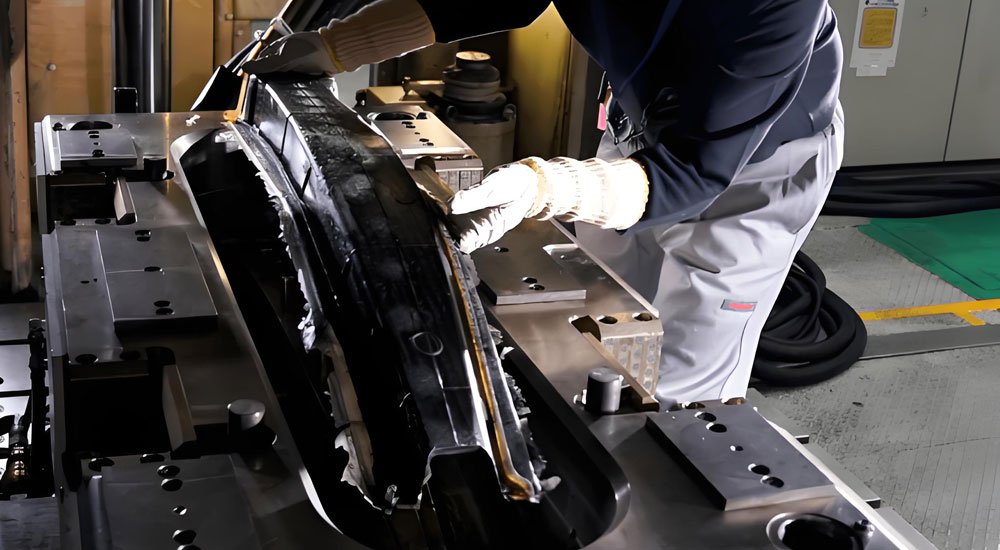
Post-processing:
If required, the finished product may need further post-processing, such as trimming, sanding, painting, or other surface treatment processes, to improve the appearance quality or to fulfill other functional requirements.
Properties and Advantages of Carbon Fiber
Carbon fiber offers unique properties that make it ideal for advanced manufacturing:
- High Strength-to-Weight Ratio: It’s lighter than metals like steel and aluminum but just as strong, making it perfect for applications where weight reduction is critical.
- Corrosion Resistance: Carbon fiber does not rust or corrode, extending the lifespan of components.
- Thermal Stability: It can withstand high temperatures without losing its strength, making it reliable in extreme conditions.
- Design Flexibility: It can be molded into complex shapes, providing unmatched design versatility.
- Excellent dimensional accuracy: Due to the high precision of the molds, molded products usually have good dimensional control.
Methods for Manufacturing Carbon Fiber Parts
There are several techniques to produce carbon fiber parts, each tailored to the specific needs of the product.
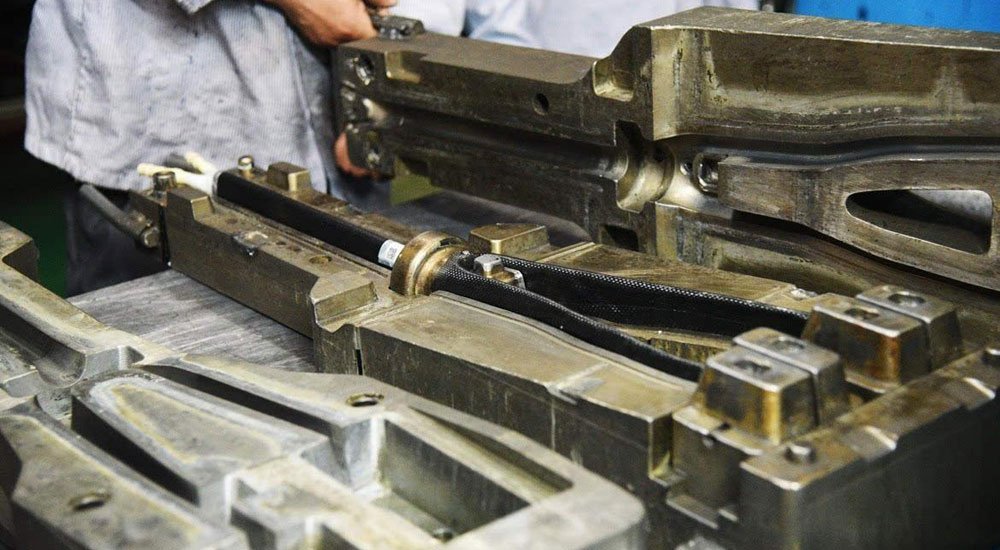
Carbon fiber fabric is layered into a mold and combined with resin to create rigid parts. This process often uses high-pressure presses or autoclaves for precision shaping.
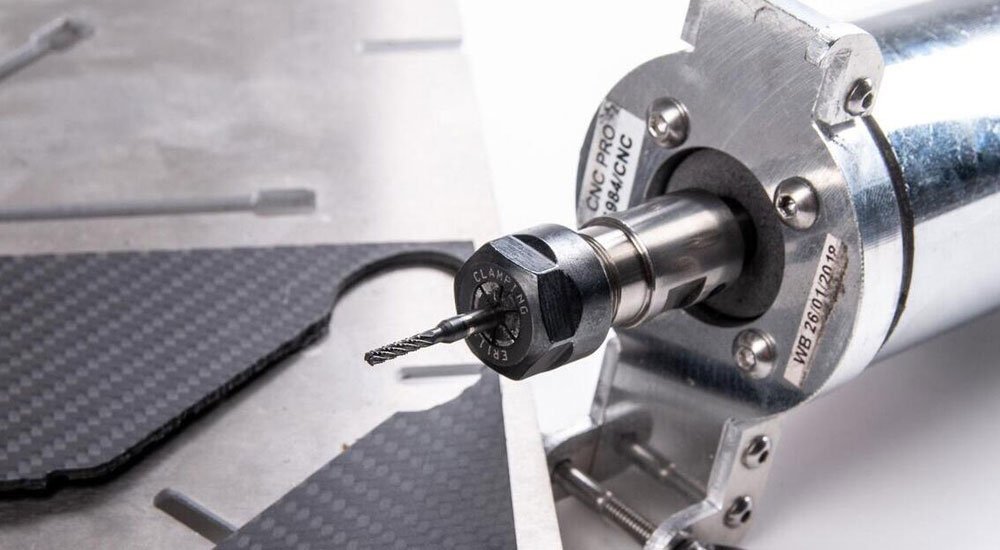
Once the carbon fiber material is cured, CNC machining can be used to trim and refine parts with tight tolerances, ensuring accuracy for intricate designs.
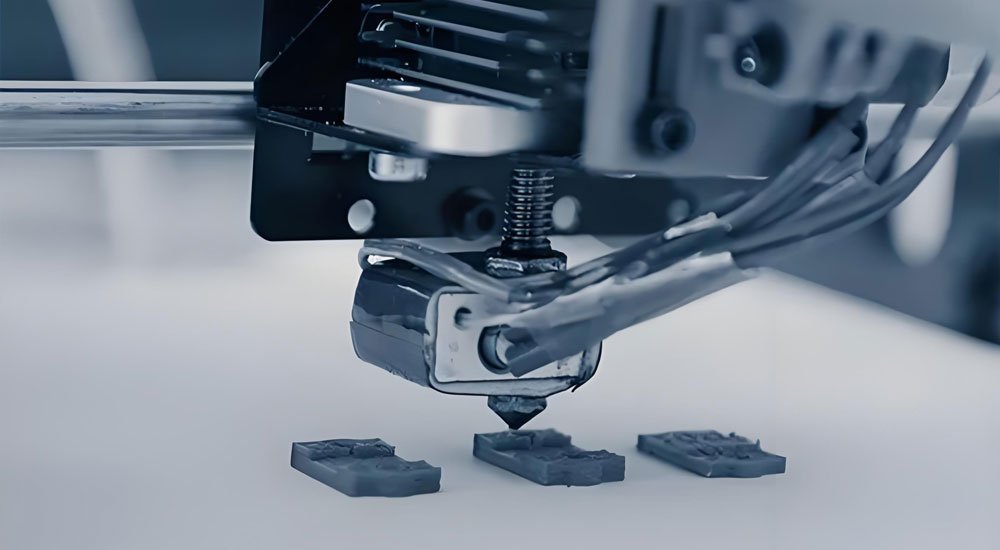
For rapid prototyping and small-scale production, 3D printing with carbon fiber-infused filaments is a growing technology. This allows for fast, custom parts with enhanced strength properties.
Applications of Carbon Fiber Parts
Carbon fiber is used in various industries due to its unique qualities:
- Aerospace: Lightweight yet strong components for aircraft structures.
- Automotive: High-performance parts that reduce weight and improve fuel efficiency.
- Sports Equipment: Durable and light materials for bicycles, tennis rackets, and more.
- Medical Devices: Tools and prosthetics that benefit from carbon fiber’s strength and lightness.
Automotive Carbon Fiber Parts Expertise at M.P.M.
At M.P.M., we specialize in manufacturing custom carbon fiber parts for the automotive and motorcycle industries. Our capabilities include:
Automotive Components: Hoods, spoilers, diffusers, and interior trim pieces designed for performance and aesthetics.
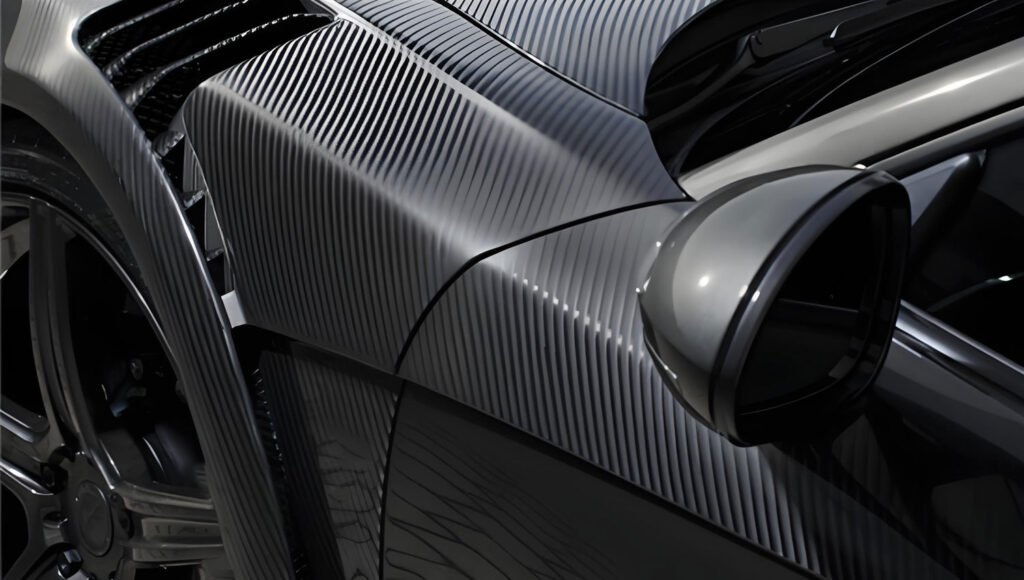
Motorcycle Parts: Fairings, frames, and fuel tanks for enhanced durability and weight reduction.
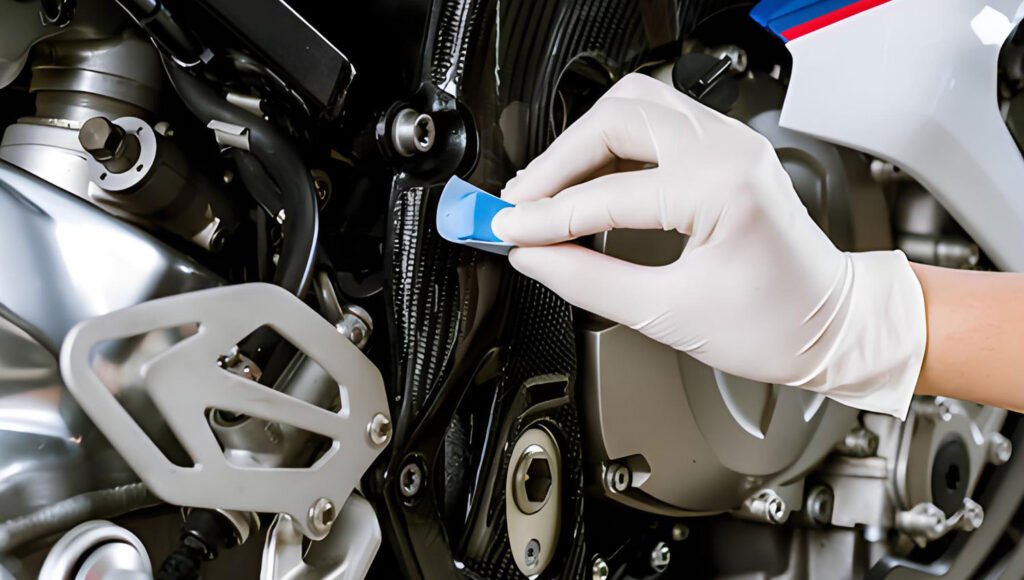
Why Choose M.P.M. for Carbon Fiber Parts Manufacturing?
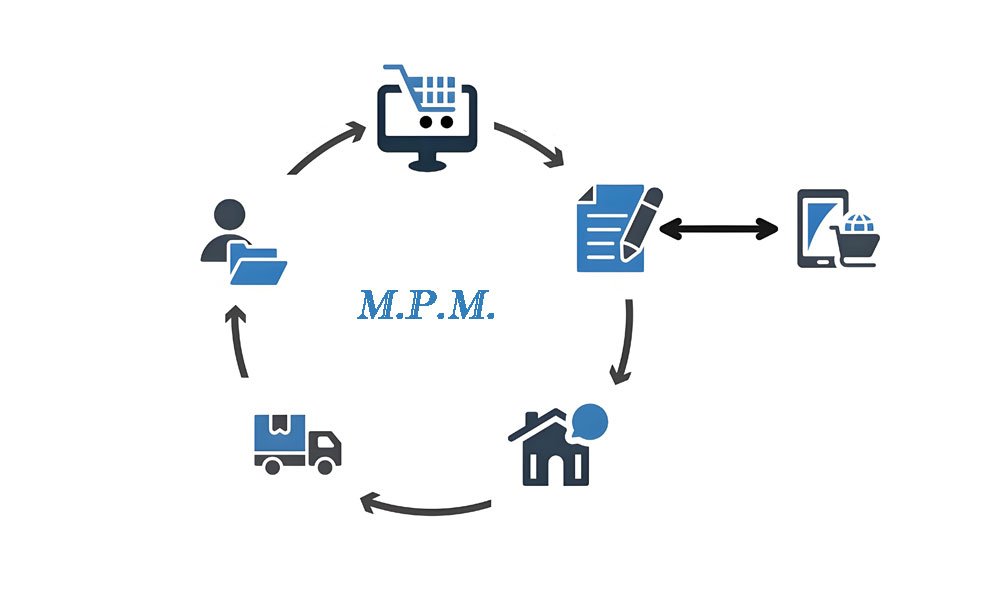
From concept and design to production and assembly, we offer a complete service.
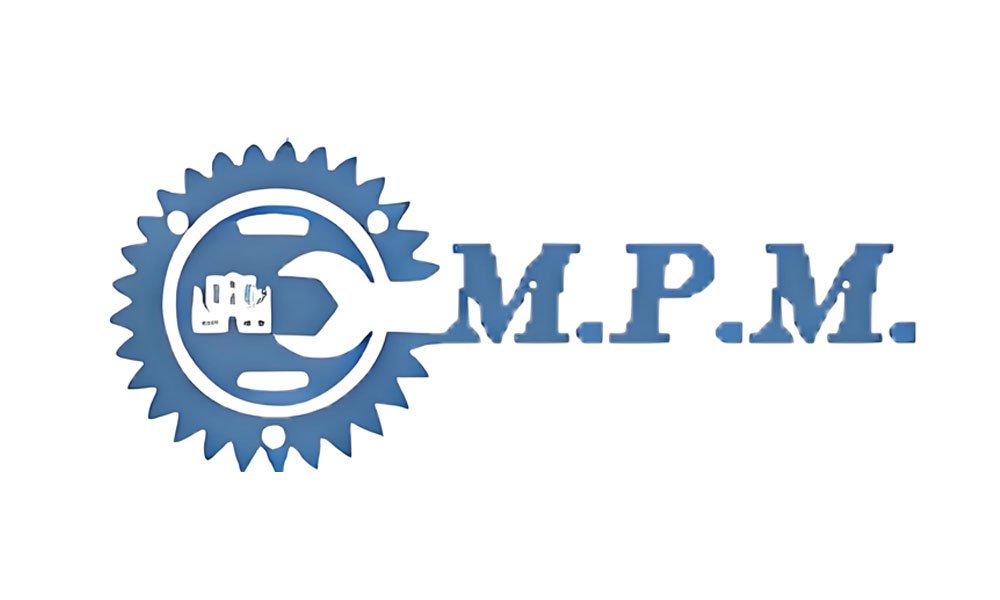
Our team works closely with clients to create bespoke solutions to specific needs.
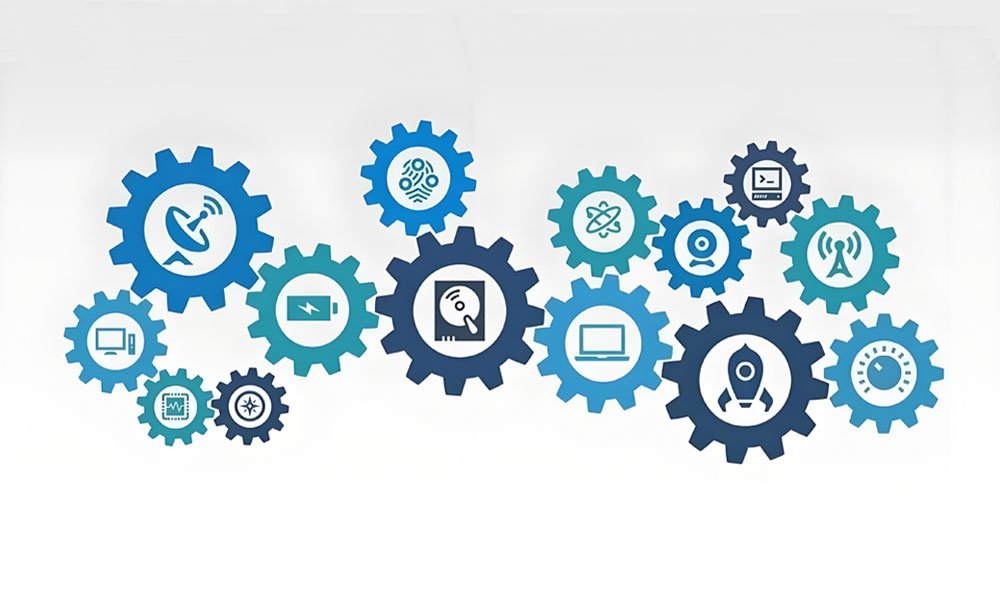
With years of experience, we produce high-precision parts that meet top performance standards.
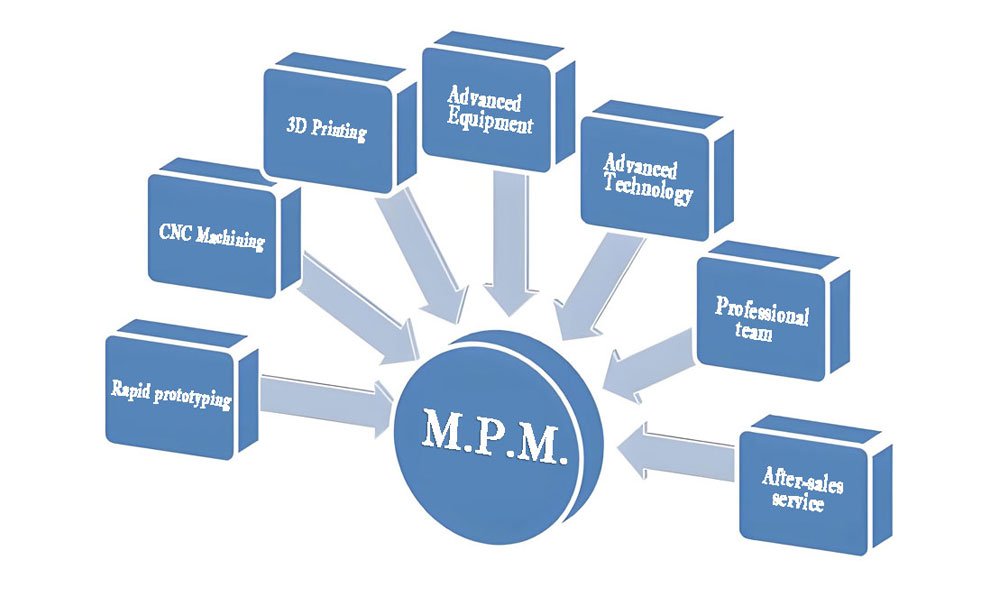
We use state-of-the-art equipment and processes, ensuring accuracy, efficiency, and reliability.
FAQ
How long does it take to manufacture a carbon fiber part?
The timeline varies depending on the complexity and size of the part, but typically ranges from a few days to a couple of weeks.
Are carbon fiber parts more expensive than metal parts?
Yes, due to the specialized processes and materials involved, but the performance benefits often outweigh the initial cost.
Can carbon fiber parts be repaired?
In many cases, yes. Small cracks or damage can often be repaired, but larger structural issues may require part replacement.
What are the limitations of carbon fiber?
While carbon fiber is incredibly strong, it is brittle and can crack or break under certain high-impact conditions.
What are the disadvantages of carbon fiber molding?
- High equipment cost: The manufacturing cost of the mold is high, especially for complex shapes or large size products, the initial investment is large.
- High process complexity: The control of process parameters (temperature, pressure, curing time, etc.) requires a high degree of control, and any slight error may affect the performance of the final product.
Explore Our Other Services
M.P.M. offers a complete range of manufacturing services!Explore more about our capabilities in:
Investment Casting
Parts of complex shapes and sizes can be cast; the flexibility of almost any metal material can be increased
CNC Machining
CNC machining can produce high-precision parts with a variety of features and tolerances as low as ±0.001mm.